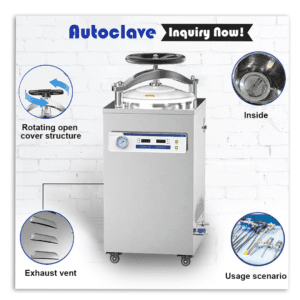
An industrial autoclave functions as a massive sterilization machine that uses high-pressure steam to sanitize large quantities of items. Industrial autoclaves differ from smaller dental and laboratory autoclaves as they are designed to meet bulk sterilization requirements which makes them ideal for hospitals research facilities and manufacturing plants. The industrial autoclave achieves sterilization by heating steam to temperatures higher than 100°C (212°F) which allows it to destroy bacteria, viruses, spores and various pathogens.
Industrial autoclaves are vital for several reasons:
High volume processing capabilities enable these machines to simultaneously process large quantities of items which makes them a perfect fit for both busy healthcare settings and manufacturing environments where efficient operations are essential.
Industrial autoclaves utilize high-pressure steam to achieve complete sterilization which lowers healthcare-associated infection risks and maintains manufacturing product safety.
Various industries follow strict sterilization rules which are necessary for regulatory compliance. Industrial autoclaves serve as dependable systems to meet necessary compliance standards.
Batch autoclaves operate by processing predetermined amounts of items during each cycle. Healthcare settings use these autoclaves to sterilize surgical instruments while laboratories utilize them to sterilize media and equipment. The design of batch autoclaves allows them to be vertical or horizontal based on specific space requirements.
Continuous autoclaves facilitate high-throughput sterilization processes by design. These devices enable constant loading and unloading which suits manufacturing settings where many products require efficient sterilization.
Steam-flush pressure pulse autoclaves achieve better sterilization efficiency by employing both steam flushes and pressure pulses. This autoclave type successfully sterilizes both complex instruments and porous materials through comprehensive steam distribution.
Double-door autoclaves serve environments that require strict contamination control measures. These autoclaves have two distinct doors with one designated for loading and another for unloading to maintain separation between sterilized products and unsterilized areas. The design of double-door autoclaves proves especially advantageous when used in sterile processing departments.
Contemporary industrial autoclaves include sophisticated control systems which enable accurate tracking of temperature, pressure levels and the duration of sterilization. The advanced control systems within industrial autoclaves maintain effective sterilization cycles through consistent monitoring.
Numerous industrial autoclaves have user-friendly digital displays which show up-to-the-minute information about the sterilization process. Staff members can easily operate autoclaves and monitor their performance through intuitive interface designs.
The automated cycle programs allow users to choose precise sterilization configurations depending on the materials being treated. The feature increases operational efficiency while maintaining uniform outcomes throughout various sterilization cycles.
Industrial autoclaves can capture detailed records of sterilization cycles through data logging functions which aid in compliance adherence and quality control documentation. Industries that operate under regulatory requirements find this feature indispensable.
Effective sterilization depends on loading the autoclave correctly. Operators must position items so steam moves unobstructed through the chamber and always put heavier items at the bottom. Do not fill the chamber beyond its capacity because full loads restrict steam flow which results in poor sterilization.
To achieve optimal performance industrial autoclaves require consistent maintenance and calibration. Perform routine inspections to identify signs of wear and tear while verifying that temperature and pressure settings remain accurate.
Staff members who operate the autoclave must receive proper training. Staff needs to understand how to operate the autoclave including its features, loading methods, and safety procedures to achieve reliable and secure sterilization results.
Establish a regular validation protocol to evaluate sterilization cycle performance. The autoclave’s operational status should be confirmed by conducting biological indicator testing alongside chemical indicator checks and physical monitoring.
The extreme temperatures and pressures of autoclaving make it impossible for certain materials to endure the process. To avoid damaging instruments and materials it is vital to verify their compatibility with autoclave sterilization methods.
Poor air evacuation from the autoclave limits steam penetration which leads to ineffective sterilization. Successful sterilization requires both proper functioning of the autoclave and effective air elimination.
Sterilization protocol compliance proves difficult when environments operate at high capacity. Both regular monitoring and documentation are required to maintain best practice standards and regulatory compliance.
Proper operation and installation conditions for industrial autoclaves demand sufficient available space. Facilities need to maintain adequate space for operating these devices and conducting secure loading and unloading activities.
Various industries depend on industrial autoclaves to maintain the sterility of medical instruments and equipment. When medical device distributors and procurement specialists study industrial autoclave types and their features along with best practices for use they can select sterilization equipment with informed decision-making. The use of effective sterilization protocols boosts patient safety and product quality while increasing operational efficiency.
Our team is available for more details about industrial autoclaves and sterilization best practices.
The primary function of an industrial autoclave is to sterilize medical instruments, equipment, and products using high-pressure steam to eliminate harmful microorganisms.
When choosing an industrial autoclave, consider factors such as the volume of items to be sterilized, the types of materials being processed, and available space. Continuous autoclaves are suitable for high-throughput needs, while batch autoclaves are ideal for smaller loads.
Industrial autoclaves should be maintained regularly, with routine inspections and calibrations recommended at least once a year. However, more frequent checks may be necessary depending on usage.
Biological indicators are used to verify the effectiveness of sterilization cycles by introducing a known quantity of resistant spores. They are essential for validating that the autoclave is functioning correctly.
No, not all materials can withstand the high temperatures and pressures of autoclaving. It is important to check the compatibility of instruments and materials before sterilization.
For inquiries, please contact us at inquiry@shkeling.com or reach out via WhatsApp at +8618221822482. Visit our website for more information: Keling Medical.
Sterile conditions remain fundamental in dental practices to protect patients while meeting health regulatory standards. Dental clinics rely on autoclaves to sterilize their instruments and equipment which eradicates dangerous microorganisms.
Maintaining sterile conditions for dental instruments and equipment remains essential to protect patients and comply with health standards. Dental sterilizers serve as essential equipment that removes dangerous microorganisms from dental
The dental field requires sterile environments to ensure patient safety and to meet health regulation standards. Dental autoclaves serve as dedicated sterilization machines that destroy harmful microorganisms on dental equipment
The healthcare and manufacturing industries require sterile environments to ensure safety and meet industry standards. Industrial autoclave machines serve as sophisticated sterilization devices which use high-pressure steam to sanitize medical
Maintaining a sterile environment is essential for safety and regulatory compliance in healthcare and manufacturing industries among others. Industrial autoclaves represent sophisticated sterilization systems that utilize high-pressure steam to eradicate
The healthcare sector demands efficient sterilization methods above all else. Large autoclaves maintain the sterility of medical instruments and equipment by eliminating dangerous microorganisms. These devices manage substantial loads of